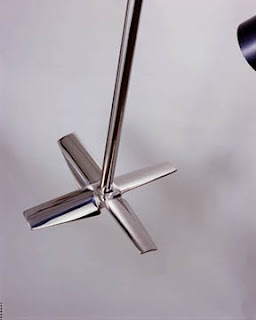
Shaft strength is determined by the section modulus of the shaft.
SOLID SHAFTING has been the most common choice among other mixer manufacturers for many years because of availability, ease of construction and the fact that many impeller hubs require a key to transmit torque. These hubs slide onto the shaft and are held in place with a key and set-screw. The disadvantage of keyed one-piece hubs is that they can be difficult to service, steady bearings must be disassembled to allow clearance for impeller removal, and the impeller will usually weigh more due to the required thickness at the bolted blade attachment area. This extra weight coupled to the heavier solid shaft equates to a greater thrust load on the mixer bearings, limiting bearing life.
HOLLOW SHAFTING is Sharpe Mixers' preferred choice due to the design advantages offered, increased availability, and innovative methods of attaching impellers to the shaft without the use of key-ways, like our split hub design. Comparing a solid shaft with a hollow shaft of equal section modulus, both will transmit torque with equal stress levels, but the hollow shaft will be stiffer, or rather will deflect less under the same overhung moment. This translates to longer allowable shaft lengths at a given stress level, and less weight at a given shaft length. Less weight means less thrust transmitted to the drive bearings, and a longer expected bearing life. Less weight and higher stiffness also helps avoid critical speed, frequently a limiting factor in mixer design.
Regardless of the style of shafting used on a mixer, the important concern is that it is designed correctly for the application. Many factors regarding the tank and process enter into the design of a mixer shaft. Let us determine the best design for you today!
Great article Don!
ReplyDeleteMany people think of hollow shafting as weaker than solid, without realizing that the "equivalent" hollow shaft is larger in diameter than the solid. Just like racing bicycles that use large diameter tubing for the frame, larger hollow shafting is lighter, stonger and stiffer.
Below is an example of an engineering analysis that explains why:
_____________________________________________
SHAFTING, Hollow vs. Solid Sect. 6, pg. 51.01
Earlier in this section it was stated, “When comparing a solid shaft with a hollow shaft of equal section modulus, both will transmit the torque with equal stress levels, but the hollow shaft will be stiffer, or rather will deflect less under the same overhung moment”. The following is an engineering analysis to support this statement:
Section modulus = Where I = Moment of Inertia
c= Distance to extreme fiber
Hollow Shaft : O.D.= 6.625”, I.D. = 5.761”
Moment of inertia for hollow shaft = = 40.4904
Section modulus for hollow shaft = = 12.2
4.99” dia. Solid Shaft:
Moment of inertia for 4.99” solid shaft = = 30.4349
Section modulus for 4.99” solid shaft = = 12.2
Deflection on simple cantilevered beam:
Max Deflection =
Where P= 50 lbs
l= 100 inches
E= 30,000,000
I= Moment of Inertia
Hollow Shaft Deflection = = 0.01372” WT.= 29.1lbs/ft
4.99” Solid Deflection = = 0.01825” WT.= 67.8lbs/ft
(33% more deflection) (132% heavier)